Overview of the project
This project lead to the creation of two haptic cable-driven parallel robots (CDPR): a 3-dimensional prototype with a hybrid configuration that allows it to reconfigure in real time (see below); and a 2-dimensional multimodal haptic interface able to present force and visual feedback, as well as texture (through vibrations) and friction.
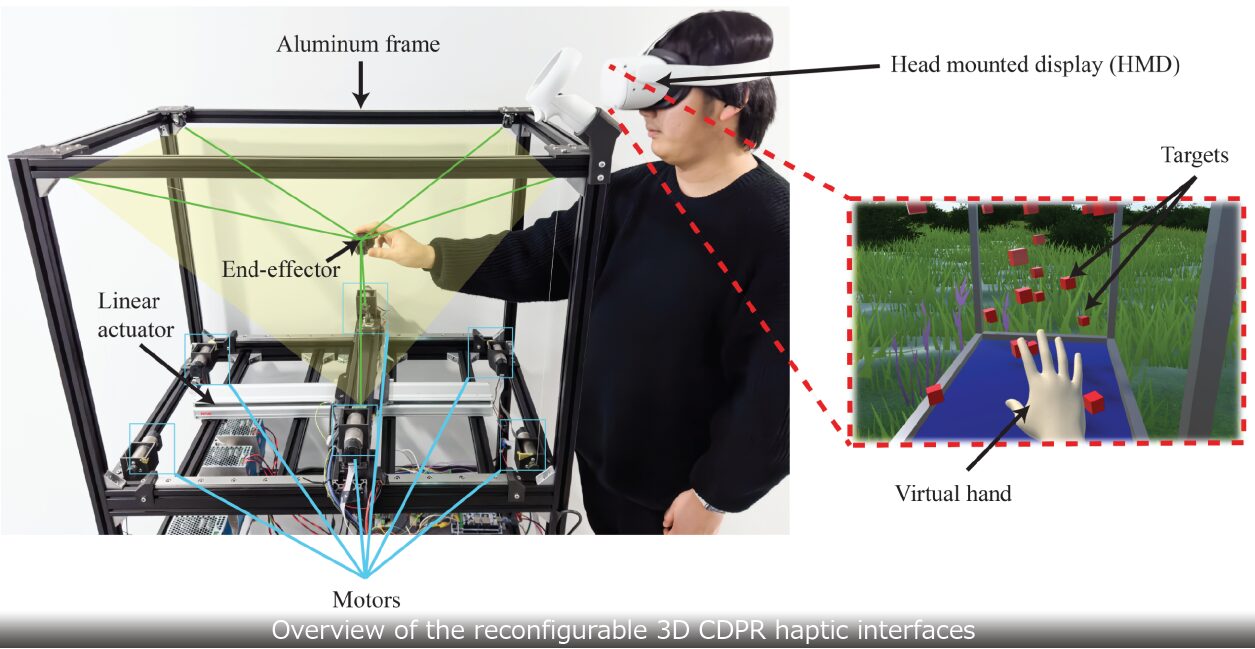
The purpose of 3-dimensional interface (see above) was to clarify the advantages that a variable structure can provide for haptic interaction. In this regard, experimental and theoretical results regarding the device’s workspace and its force feedback capabilities were presented. The comparison of the variable and the usual cable configuration showed that feedback accuracy is maintained in both cases and, more importantly, that the force exertion capabilities of the haptic devices are maximized when the device has only four cables with moving anchor points. In this case, the workspace available for haptic feedback is optimized and the force exertion capabilities are isotropic, i.e. the Tension Index is higher (see figure below).
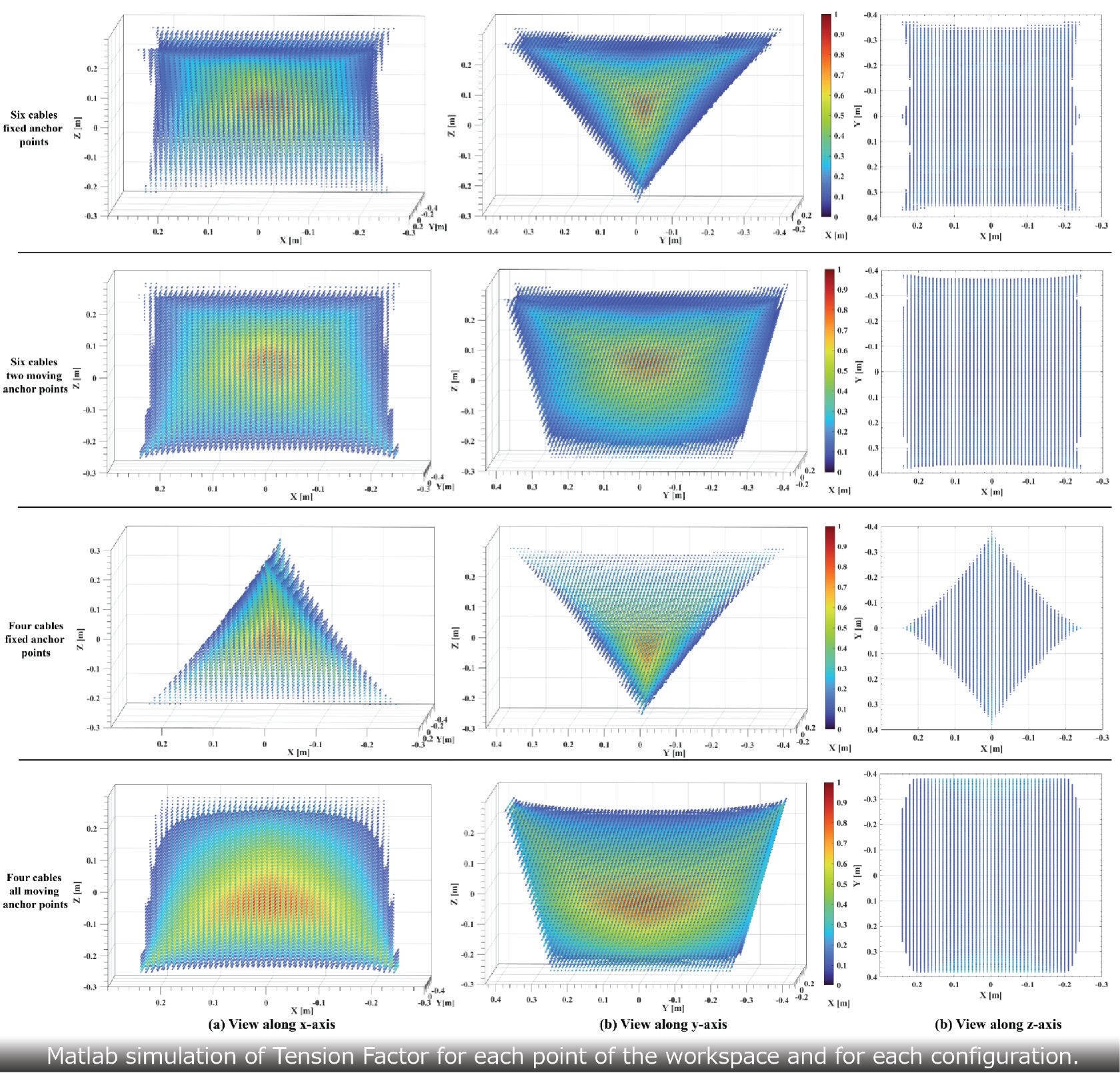
Additionally, another experiment was conducted to study changes in user performance both objectively and subjectively when using both the variable and the usual cable configuration. The results showed that feedback accuracy is maintained, and there are no drawbacks to using hybrid configurations (see links to the publications at the bottom of the page).
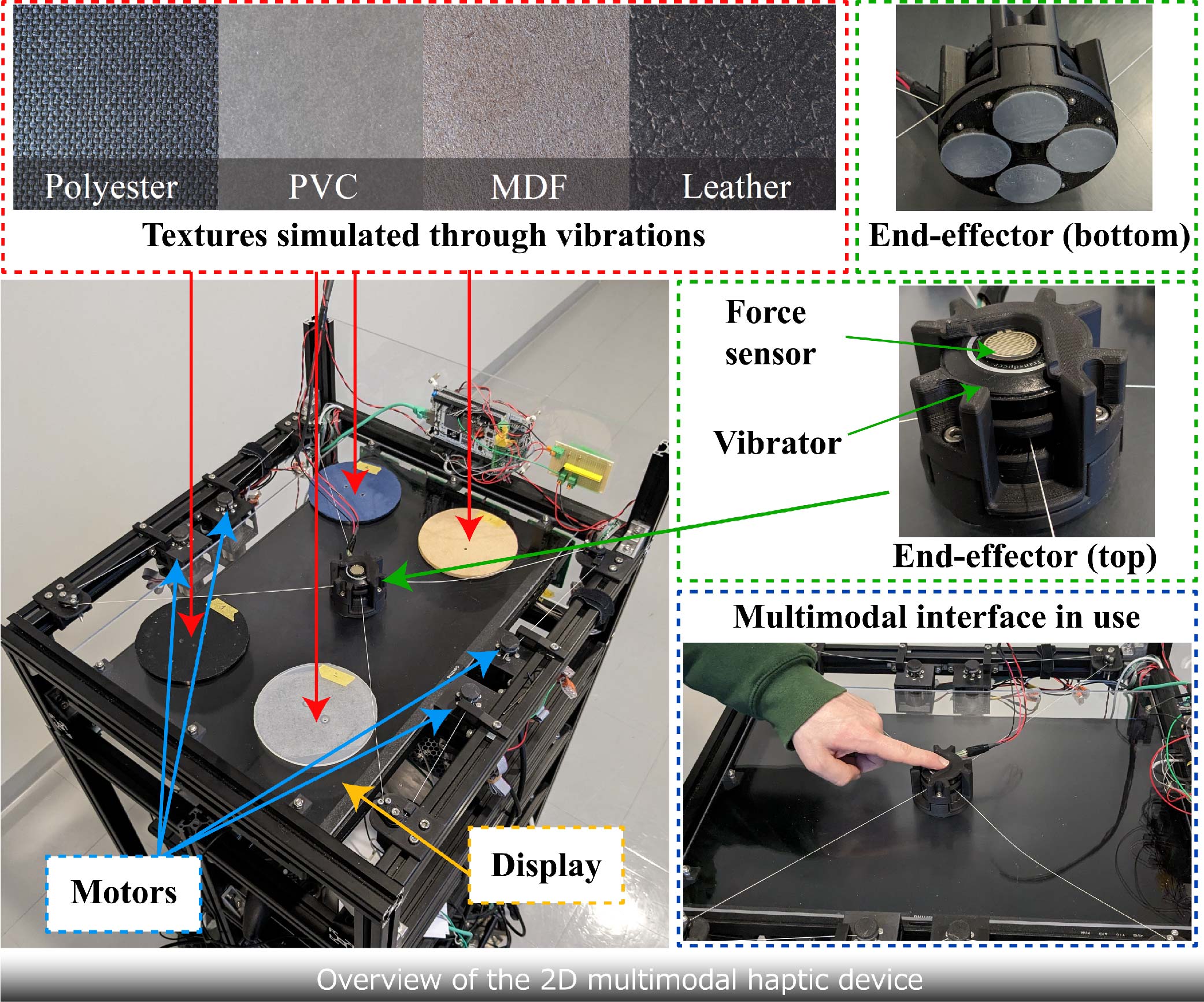
Regarding the 2D Multimodal haptic interface, its purpose is to present several types of haptic stimuli (visuals, force, texture with vibrations, and friction) by integrating them into the end-effector of a planar cable robot. It is still a work in progress towards the final goal of this research which is to design a fully reconfigurable 3D multimodal interface. Nonetheless, a control scheme was designed (see figure below) and preliminary results were obtained through a user-based experiment.
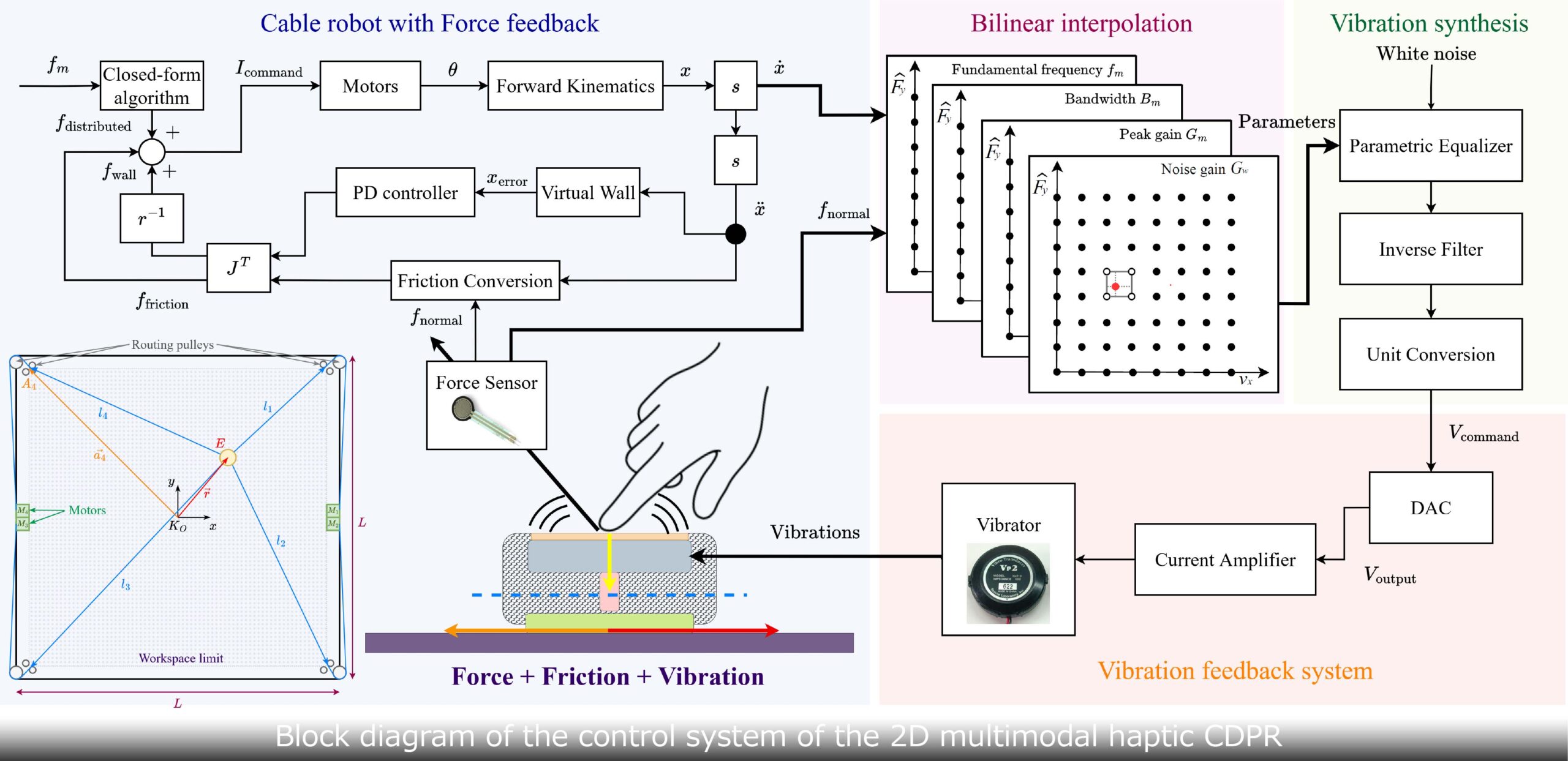
The control system can be divided in four main parts. First, the force feedback which sums three different signals: the friction, the virtual wall feedback and the minimal tension required to prevent the cables from slacking (the virtual wall is used to keep the effector close to the center of the workspace). The friction is calculated from the normal force measured by a pressure sensor. Finally, the vibration feedback system is Parametric Equalizer or PEQ-based (see this work by Tozuka et al. and this page for more information on vibration generation). According to the operator’s current speed and force, a bilinear interpolator uses the four nearest data points to calculate a set of parameters, and then generate vibrations corresponding to each texture. The combination of all the signals provides the necessary stimuli for multimodal haptics.
Author of this study
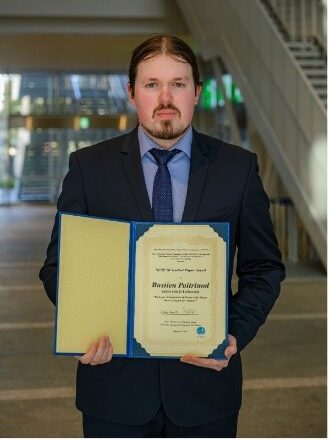
Bastien Poitrimol, 3rd year doctoral student.
He entered Supmicrotech – Ensmm in 2016, then joined Tokyo Denki University through a double degree program in 2019. He completed both master’s program in 2021. He entered the doctoral program of Tokyo Denki University in 2021 and is currently in his third year of doctoral studies.
Research Area: Cable Robots, Parallel Robots, Haptics, Virtual Reality, Robotics
Related Publications
Poitrimol, B., and Igarashi, H. (April 15, 2024). “A Cable-Based Haptic Interface with a Reconfigurable Structure.” ASME. J. Mechanisms Robotics. doi: https://doi.org/10.1115/1.4065318
B. Poitrimol and H. Igarashi, “A User Study of a Cable Haptic Interface with a Reconfigurable Structure,” 2023 IEEE World Haptics Conference (WHC), Delft, Netherlands, 2023, pp. 460-466. doi: https://doi.org/10.1109/WHC56415.2023.10224379.
Poitrimol, B., Igarashi, H. (2023). A Cable-Based Haptic Interface with a Reconfigurable Structure. In: Caro, S., Pott, A., Bruckmann, T. (eds) Cable-Driven Parallel Robots. CableCon 2023. Mechanisms and Machine Science, vol 132. Springer, Cham. doi:https://doi.org/10.1007/978-3-031-32322-5_36